The latest blog in our ongoing series explores material use and resource efficiency potential in India's e-vehicle sector
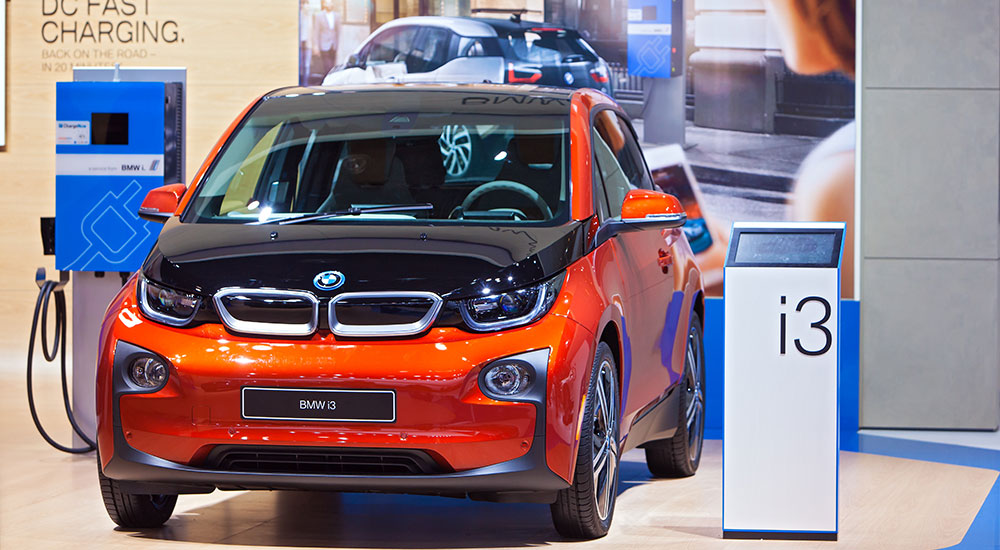
The automobile industry in India is one of the key sectors driving the country’s economic growth. However, vehicular emissions are also a large contributor to airborne pollution[1]. The Indian government is pushing for increased market penetration of electric vehicles (EVs) in the country as an attractive alternative to conventional internal combustion engine (ICE) vehicles. They are also a way to curb pollution and reduce import of crude oil. Various policy measures such as Faster Adoption and Manufacturing of (hybrid &) Electric Vehicles in India (FAME India) under the National Electric Mobility Mission (NEMM) in 2015 have been instituted. In Budget 2019, the government allocated Rs. 10,000 crore to the FAME II scheme besides announcing a tax deduction of Rs. 1.5 lakh on the interest paid on loans taken to buy EVs. It is also suggesting the GST council to reduce the tax rate on EVs from 12% to 5%.
The Economic Survey of India 2019 also emphasises on the need for India to emerge as a hub of EV manufacturing. It highlights the need for a policy push to devise universal charging standards for India and to provide adequate charging infrastructure.
The FAME I scheme was successful in increasing the share of hybrid and electric passenger vehicles sales from almost 0% in 2012 to 1.3% by 2016. In February 2019, the government announced that it would offer $1.4 billion in subsidies for both buyers and manufacturers of EVs and also impose higher import tariffs to promote domestic automotive companies to manufacture EVs. At present, only two Indian auto companies manufacture these vehicles – Tata Motors and Mahindra. Hyundai has recently launched their first electric vehicle (Kona) in India. Kia Motors, a new entrant in the India car market, is developing electric fleets designed specifically for this market. It had also signed a memorandum of understanding (MoU) with the Andhra Pradesh government last year to aid the growth of electric mobility in the state.
Meanwhile, many cities such as Hyderabad, Chennai, Guwahati, Kolkata, Bengaluru, and Jaipur have already undertaken trials of electric buses which will soon be plying regularly. India also aims for 30% of its public transport to go electric by 2030.
Resource use and efficiency
The growth in e-mobility will result in material requirements (particularly lithium, rare earths, flame-retardant and thermoplastics). India has very little known reserves of lithium and it imports nickel, cobalt, and battery-grade graphite which are all crucial components in battery manufacturing. Unavailability of rare earth materials used to manufacture magnets for EV motors is a constraint. Vulnerability of supply due to relying on imports of these materials can pose a major challenge and impede the growth of EV sector in India.
Resource efficiency is an important way to address this challenge and can be integrated across lifecycle stages of EVs. Designing for greater dismantling and effective disposal will enhance recovery of parts that could be used for remanufacturing. Vehicle design that is receptive to using recycled/secondary raw material will reduce the chances of down-cycling of recovered material from end of life (EoL) vehicles. This should be accompanied by focusing on highly efficient and lightweight materials that may reduce energy footprint of vehicles per kilometre.
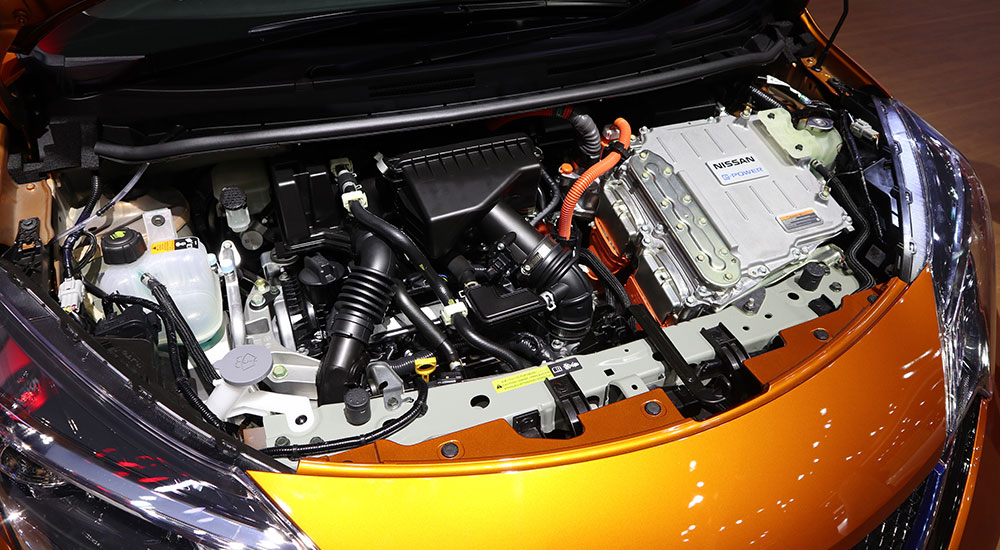
Addressing material criticality issues
Lithium has been the choice of material for EV batteries. However, solid state battery technology that uses solid electrodes and a solid electrolyte instead of the liquid or polymer electrolytes found in lithium-ion (Li-ion) or lithium polymer batteries is also emerging as a cost-effective way to potentially reduce high import dependence for lithium. Breakthroughs have also been achieved in the use of sodium ion batteries (SIBs) that have been considered as a promising alternative for the next generation of electric storage systems. This is due to similar electrochemistry to Li‐ion batteries and the lower costs of sodium resources.
Finding ways to reduce the use of rare earths is particularly important for the sector as many motors in EVs rely on permanent magnets containing rare earths. India is heavily import-dependent on countries such as China for these materials. Currently, there is a lot of demand for high-performing Neodymium Iron Boron (NdFeB) magnets. It then becomes important to push for better material efficiency and larger adoption of motors that are free of rare earths. Reducing the use of NdFeB magnets will also have environmental benefits in the form of reduction of greenhouse gas emissions.
Further, by moving many parts of power electronics (that include inverters, bi-directional DC converters, and chargers for plug-in EVs) closer together and integrating into fewer modules offers substantial potential in terms of raw material savings and increasing efficiency. For instance, if we look at the weight of cables used in EVs and total number of parts used in EV models, we observe a decrease in both cable weight and number of parts in the latest models, reflecting a higher integration of more recent EV powertrain systems. Further, hydrogen fuel cell powertrains in the future could provide significant weight and space saving advantages over battery electric ones for heavy-duty trucks.
During the use stage, EVs enable load equalisation of power systems. Since EVs could be charged at non-peak hours, the non stockable energy of these hours along with the power generation facilities can be effectively and efficiently utilised, contributing to saving energy resources. Given that India is moving significantly towards its ambitious renewable energy targets, low cost storage with such options needs to be harnessed in the future.
At the end-of-life (EoL) stage, opportunities for reusing components, particularly giving used batteries a second life in renewable energy storage applications is important. However, sourcing back of used batteries and other materials from EVs will require effective and viable development of a robust reverse logistic network and recycling infrastructure. India has duly recognised the need for developing a sustainable and commercially viable EoL vehicle policy and the Central Pollution Control Board (CPCB) had issued guidelines to regulate the sector in an environment-friendly manner.
The path ahead
The Government of India needs to continue its focus on designing policies and programmes that promote and facilitate development of a resource efficient ecosystem for the EV sector in India to enable the country to become an EV manufacturing hub.
Support should be provided for research and development on using various battery chemistries, incentivising technologies and development of vehicles/components that have superior performance in terms of energy density, range anxiety, and higher commercial proposition. A conducive policy framework over and above the FAME II scheme launched in March 2019 is the need of the hour. In a study in 2018, as part of the European Union’s Resource Efficiency Initiative (EU-REI), TERI analysed the scope and potential to enhance resource efficiency and integrate circular economy thinking in the EV sector in India.
The recommendations of this study include the need to encourage material substitution and promote use of recycled materials in new vehicle fleets (EV and ICE). This can be done through setting up modest targets for using recycled materials for specific categories and extending this coverage gradually, based on discussion with agencies including Society of Indian Automobile Manufacturers and Automotive Component Manufacturers Association of India.
Further, recycling of components such as electric motors will help recover major materials like steel, aluminium, copper, among others, and needs to be pushed for. A rare earth recycling process could be established through the industrial implementation of efficient magnetic extraction processes for different technologies. Recycling channels should be set up through business models for battery collection, storage, and recycling by the manufacturer and supported by creation of a 'traceability' system to identify the owners of discarded batteries.
A disruptive improvement in carbon footprint of EVs is equally important that can be achieved through use of renewable energy for charging of batteries. This calls for developing unique business models for creating charging infrastructure that can be operated using cleaner electricity sources, thereby making e-mobility in India more sustainable.
This blog is part of a series exploring the state of material use and resource efficiency potential of various sectors in India as part of efforts by the MoEF&CC to draft a resource efficiency policy.
You can read the previous blog here.
Footnotes:
[1] Auto fuel Vision and Policy of India, May 2014