A look at options for the cement industry in the face of a possible petcoke ban
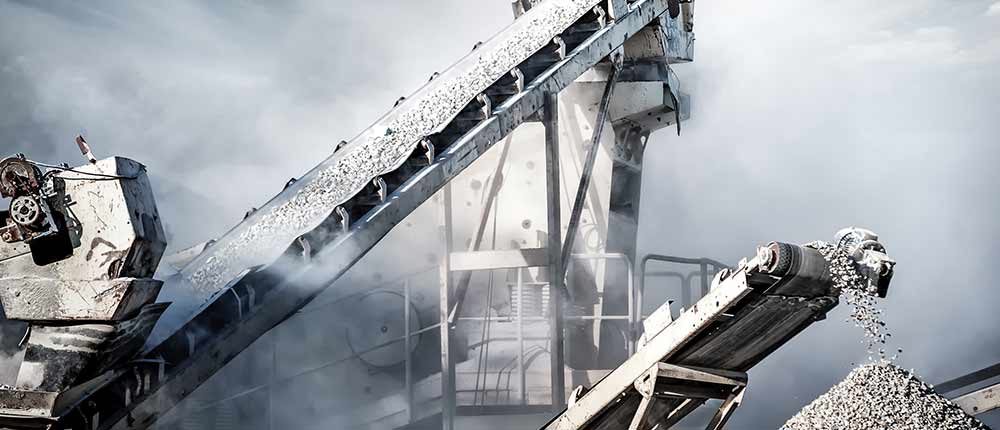
Petcoke has been under scrutiny since October 2017 when the Supreme Court first put a ban on its usage in Delhi, which it later relaxed for the cement industry. However, a nationwide ban on petcoke, or at least restrictions on its import and usage, is still not off the table. In July 2018, the Union ministry of environment told the Supreme Court that it was undertaking a study on the petcoke ban before deciding on imposing a ban on its import1.
Energy consumption is a fundamental indicator of a country's social and economic development. Broadly, our industrial sector is one of the largest consumers of energy (> 270 million tons of oil equivalent or MTOE). It includes energy intensive industries like iron and steel, chemical, textiles, aluminium, fertilisers, cement, and paper and pulp, which together account for more than half of the energy consumed. It is for such industries that petcoke, along with low-cost coal, and furnace oil, serves as primary fuel. These industries thus account for a large amount of carbon dioxide (CO2) and particulate matter emissions in India.
The cement industry
Over 70 per cent of the fuel requirement of cement manufacturers in India is met through petcoke. Cement manufacturing is an emission and energy intensive process and was responsible for 218 million tons of CO2 emissions in 2013 with close to 40 per cent of the emissions resulting from combustion of fuel to operate the kilns. Historically, the cement industry used coal but in the past few decades it has moved to the cheaper and ubiquitous alternatives - petcoke and furnace oil.
Petcoke usage in the cement industry increased at a compounded annual growth rate of 24 per cent from financial year (FY) 13 - 17. Petcoke has high calorific value (34.8 Mega Joules/kg), but also contains a high amount of sulphur (5-7 weight per cent) and vanadium (up to 500 parts per million) that cause corrosion and are responsible for toxic emissions, especially in their present application as fuel for boilers/furnaces. In fact, the global cement industry contributes to five per cent of the world's CO2 emissions.
What are the options for the industry?
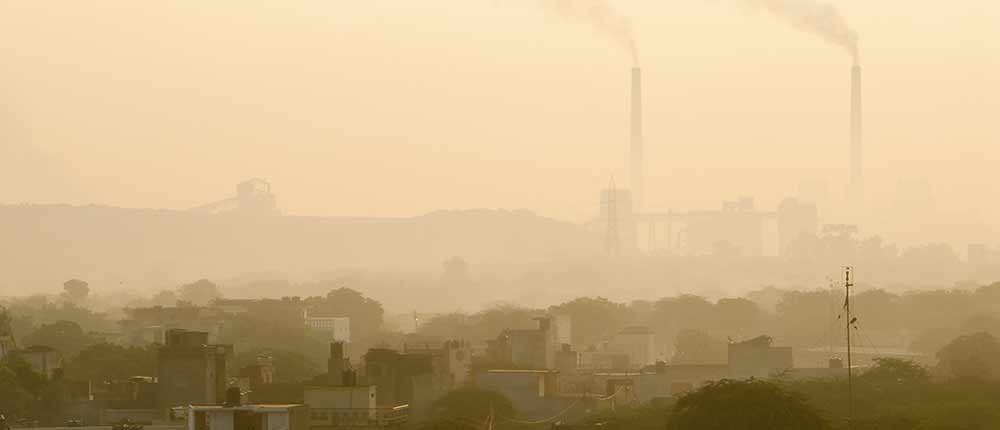
There is a need to explore a low-emission pathway powered by innovative, smart and locally relevant solutions. Moving from carbon-intensive fuels to fuels with a high hydrogen-to-carbon (H/C) ratio can reduce CO2 emissions.
While natural gas and electricity (preferably generated from renewable sources) exist as cleaner alternatives to coal or petcoke, the competitive uses and cost of generation respectively might lead to dearth in availability. Efficient fuel utilisation with reduced emissions and substitution of conventional fuels with alternative fuels is a viable two-pronged approach to reduce emissions in cement manufacturing.
Petcoke gasification, a proven thermo-chemical technology for conversion of solid fuel to gaseous fuel, can be employed for petcoke's conversion to producer gas, which is a mixture of carbon monoxide, hydrogen and methane. This can be combusted in the furnace and would yield much less particulate matter without compromising on the energy content. In addition to this, the producer gas generated from the petcoke's conversion can be converted to chemicals such as methanol and dimethyl ether (these are also alternative fuels) that emit less particulate matter on combustion. Conversion of petcoke to products such as methanol and dimethyl ether (DME) will also be point of interest for Indian refineries, where petcoke is generated as part of the crude oil refining process, as methanol and DME blending options are recommended in India's biofuel policy.
Alternative fuels can be further employed as a long-term method to bring about emission reduction. Waste materials such as agro-residues (paddy straw) and agro-industrial residues (wood chips, waste wood, rice husk, sawdust), municipal solid waste, sewage sludge, refuse derived fuel from paper and pulp industry etc. are examples of alternative fuels for application in the kiln. However, moving towards these resources is not free of qualitative and environmental challenges due to their heterogeneous nature and composition. Some examples are the high silica content (78 to 90 per cent) of rice husk ash or chlorine from polyvinyl chloride (PVC) in municipal waste. In this case, gasification and pyrolysis can be used to produce gaseous and liquid fuels of uniform quality from the above-mentioned waste streams alone or along with petcoke, which can then be used more effectively in the cement kilns.
Waste heat recovery for cogeneration of power, production of composite cement using slag and fly ash, and government push in terms of stricter emission norms will further create opportunities to establish a cleaner cement industry.
Actions required at all levels
Increasing awareness among the public and in the government about CO2 and particulate matter emissions from the cement industry is a positive development in terms of pressure to aggressively reduce the industry's emissions, which would also help mitigate the rising smog in Delhi and other cement industry hubs in India.
The use of alternative fuels is likely to raise production prices. Cement industries could also shift to imported coal. However, it is ~15 per cent more expensive than petcoke and would require a price hike of ~Rs10/bag to sustain production. This burden would likely be shifted to the end user. At present though, there is not enough clarity as to whether the cement industry's current growth rate would be able to meet the rise in price or will industries have to bear the brunt of the increased expenses to ensure that their inventories are cleared.
There is a lacuna between the policy directives and scope of implementation, which can be addressed by a continuous dialogue between stakeholders, the government and the general public. Both, improved infrastructure and public health concerns due to rising pollution have to be considered if measures such as fuel replacement are to prove successful in the long run. It is high time that energy and emission intensive industries such as cement take initiatives to start exploring and adopting clean fuels and technologies apart from their energy efficiency efforts. Technologies such as gasification and pyrolysis will play a significant role in this pursuit.
End notes: