Energy efficiency improvements among small and medium textile units in India
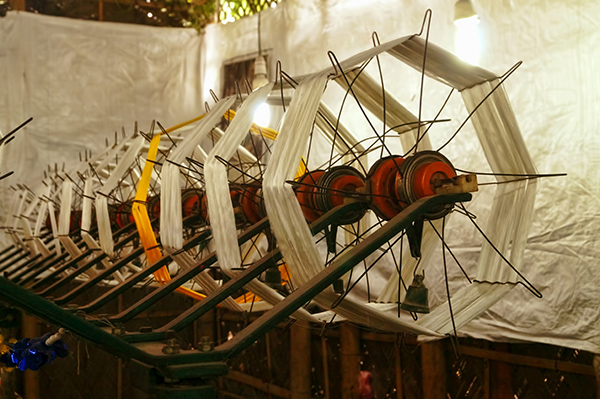
A study on ‘energy efficiency improvements among small and medium scale textile units in India’ was carried out by TERI targeting the three major energy consuming sub-sectors within textile industry, namely spinning, weaving and wet processing. The study covered surveys/interviews of textile units and key stakeholders across five clusters: Ahmedabad, Bhiwandi, Coimbatore, Surat and Tirupur.
The priorities of the study were:
1) ensuring maximum impact in terms of energy savings (targeting the most relevant processes and improvement opportunities),
2) ensuring that the medium enterprises are the main focus (but not excluding small companies when relevant) and finally, and
3) developing a strategy that can be easily scaled up.
The study found that there is a significant potential to save energy in the textile industry. Practical and economically viable energy saving opportunities in each of the three textile subsectors were identified. It was estimated that about 8% (or 2,132 million kWh per year) of energy use can be saved in spinning by widespread adoption of efficient technologies such as high speed ring frame machines, energy efficient motors, autoconer machines, invertors (variable frequency drives) and better material feeding system in blow rooms. Mainstreaming of energy efficient motors and use of day-lighting technologies like solar tubes in weaving sub-sector could save about 5% (or 734 million kWh per year) of energy. Scaling-up of energy efficient technologies such as co-generation, automation of dyeing machine control, waste heat recovery in dyeing, energy efficient automatic stenters and high efficiency pumps in processing subsectors has the potential to save 10% (or 0.69 million toe) consisting of 2,644 million kWh (0.23 million toe) electrical energy and 0.46 million toe thermal energy.